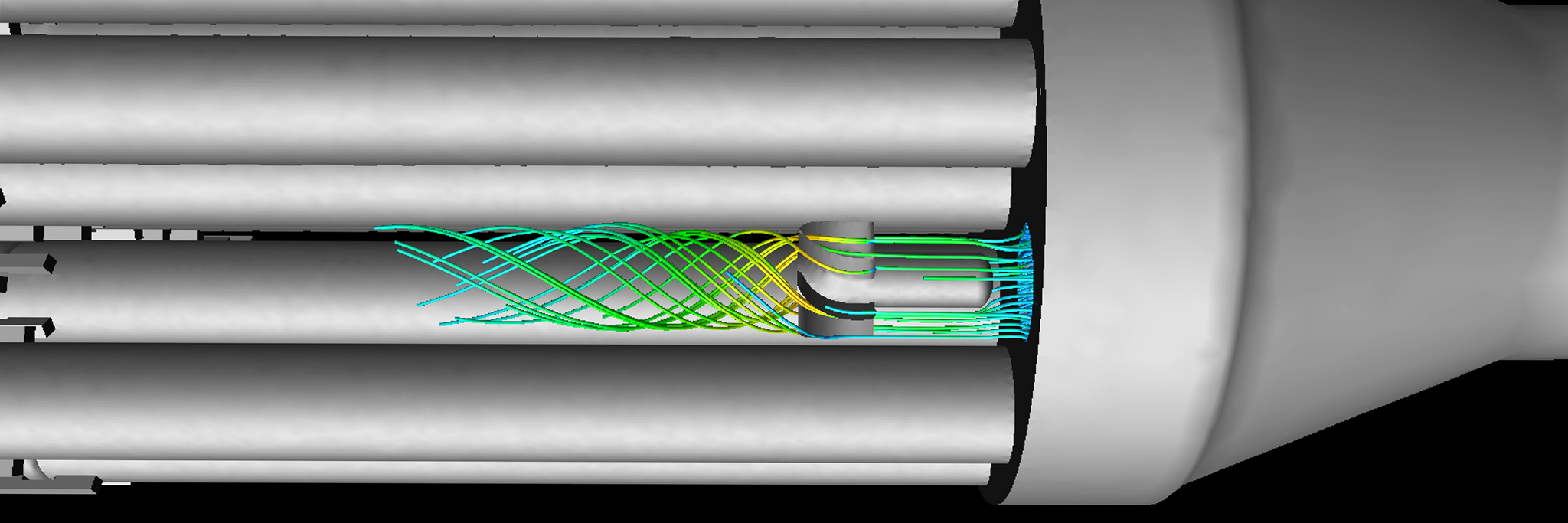
The first Vortex Tube Scrubber was patented in 1972 and has since been modified and upgraded into the technology design by Taylor Forge today. Vortex tube designs have been very influential in the development of Vertical and Horizontal 2-phase scrubbers (note: the Vertical Vortex Scrubber does not require platforms or ladders) as well as Vertical and Horizontal Knock Out (K.O.) designs to remove surges or slugs. The maintenance free vortex system reduces the size of the vessel by processing the gas faster that it would in an empty separator vessel. A vortex unit requires no shutdowns (no elements, the Vortex Scrubber operates using steel tubes) while providing effective 2 phase separation.
Vortex Tube Design
The scrubbers use a Vane entry into the internal Vortex Tubes which creates a “G” force to remove the liquids and solids from the gas. The cyclone is created utilizing the whirly jig at the vane entry position. The gas will exit out of the gas outlet while the liquids will drain into a boot or straight to storage tank downstream.
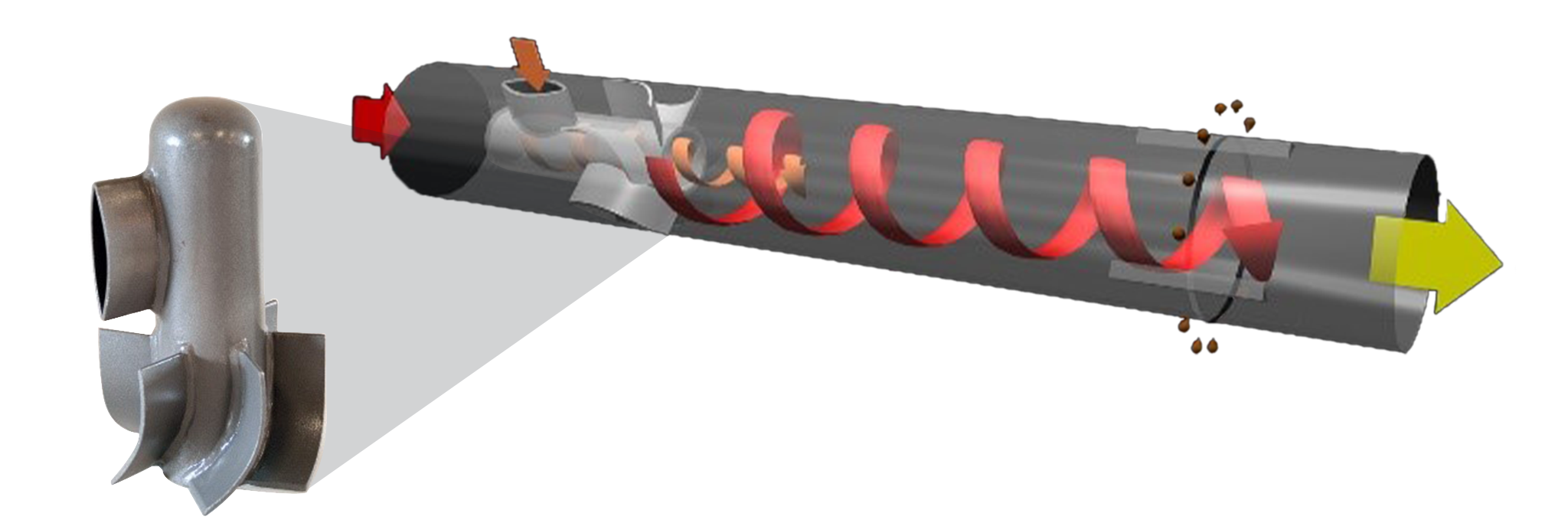
What are the best applications of Vortex Tubes? The Vortex Tube Scrubbers have a wide variety of applications within the oil and gas industry. For example, if hydrocarbons are being transported via pipeline to a processing plant, a high efficiency Vortex Tube Scrubber is preferential to protect inlet / outlet compression, and or other equipment downstream. The Vortex Tube Scrubbers offered by Taylor Forge Engineered Systems reach efficiencies of 99.9% removal of solids down to ≥ 0.3 microns and 99.9% removal of free liquids down to ≥ 1micron.
The vortex tube design works best as a scrubber where gas is already relatively dry and high efficiency separation with minimal storage capacity is required. They require little maintenance and achieve similar or better performance than your standard mesh pad, vane pack, and filter options. As such, Vortex Tube separators are the perfect scrubber in front or behind compressors, dehy’s., Fuel Gas Scrubbers, etc.
Vortex Tube Separation Applications
- Compressor after scrubbers (capable of handling excessive oil)
- Compressor Inlet Scrubbers (protects surges or slugs)
- Free Water Knockout
- Production Separators
- Flare/Vent Separators
- Overhead Accumulators
- Test Separators
- Slug or Surge Catchers
- Cooler After scrubbers
- Gas Injection
- Flash Treaters
- Steam Separators
- Well Test Separators
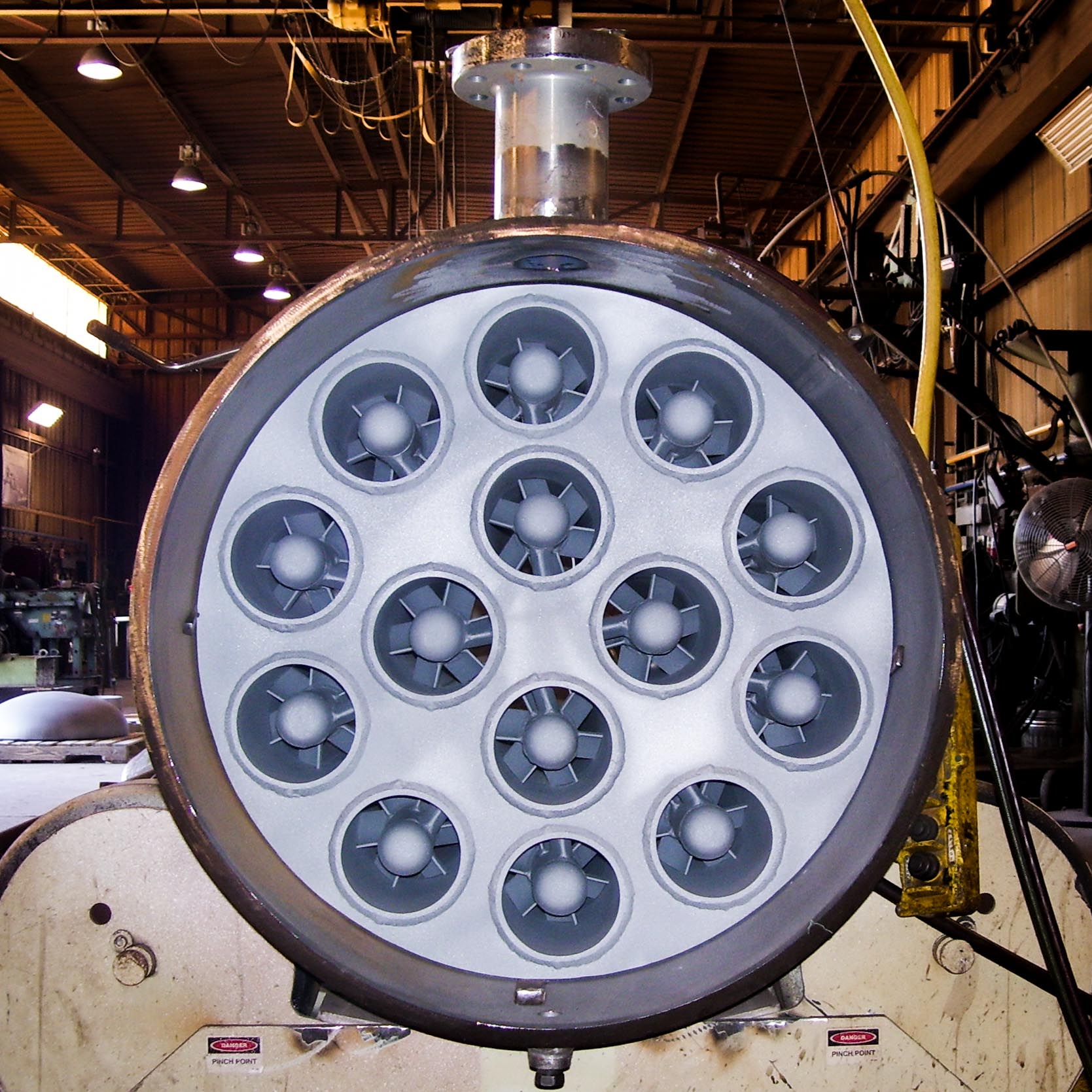
Note: What does it take to decide if vortex is right for my application? At Taylor Forge our design considerations are thorough and customizable for each specific job. Before sizing vortex tubes or clusters we begin with the operating pressure (psig) and gas flow (MMscfd). Fluid composition is also required for adequate design which include gas, oil, and water compositions, as well as phase characteristics such as mist, foam, and emulsion. Along with calculating the size of the vortex tubes and clusters, obtaining these parameters also assists with our design and placement of the vortex equipment relative to the corresponding liquid interface levels.
So you’re on a budget? Check out these 5 tips to save money on your next Slug Catcher Project.
Choosing the type of Slug Catcher equipment for your next project? This breakdown will help guide your decision.
Understanding the separation methods for your finger-type slug catcher.
WHY US
Taylor Forge Engineered Systems
has continued the reputation of traditionally dependable products
to a variety of industries.
Integrity
We don’t compromise our practices and we won’t cut corners.