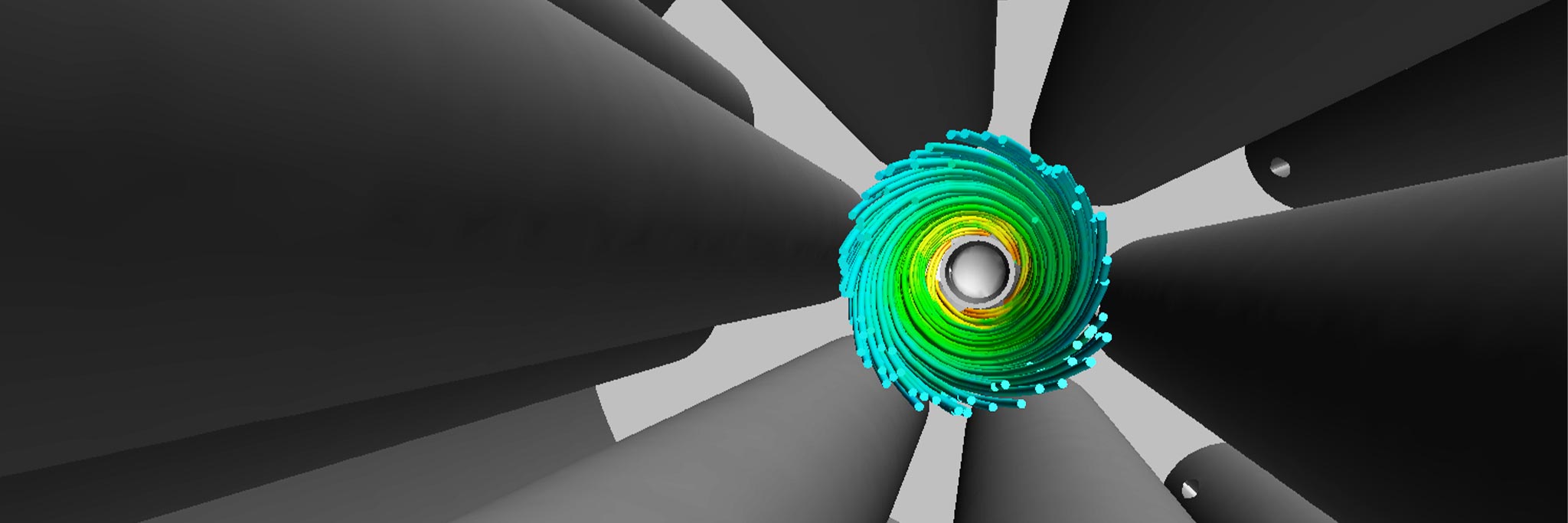
Vortex or cyclonic separation was originally developed to handle sediment in water and other low pressure fluids to separate fine particles that would otherwise negatively impact treatment facilities and equipment. As it was developed, it was found to be cost effective in a wide variety of applications. The first scrubbers were developed in 1972 and first vortex cluster was installed for ConocoPhillips at their refinery in Dubai, U.A.E, in order to stop foaming in a gas / oil separator.
Vortex uses centrifuge to push particles of a certain size to the wall using tangential force relative to the fluid in which the particles are suspended. Vortex technology also utilizes fluid levels to allow for coalescing of liquids in 2 or 3 phase separation. Additionally, its ability to quickly process gas vs residence time in standard vessels, helps shrink the size of the equipment.
So what are the best applications of vortex? Originally designed for separating lube oil out of gas lines, vortex principles and technology has a wide variety of applications within the oil and gas industry. Typically applications are identified when they include any combination of high gas flow, 2 or 3 phase fluids, high pressure differentials, and large operational ranges. While there are specific cases for bulk liquid and gas separation using vortex at mid-level efficiency, it is more likely to be used in cases where high efficiency fluid separation is needed. For example, if hydrocarbons are being transported via pipeline to a processing plant, and liquids are to be separated from gases, a high efficiency vortex separation system is preferential to protect sensitive filtration and compression equipment downstream. The vortex systems offered by Taylor Forge Engineered Systems reach efficiencies of 99.9% of solids ≥ 0.3 microns and 99.9% of free liquids ≥ 1-3 microns.
Vortex Cluster or Cyclonic Separation Applications
Vortex Cluster
- Emulsion Treaters
- Free Water Knockout
- Production Separators
- Flare/Vent Separators
- Overhead Accumulators
- Test Separators
- Slug Catchers
- Slug Separators
Vortex Tube
- Cooler Afterscrubbers
- Gas Injection
- Compressor Afterscrubbers
- Compressor Inlet Scrubbers
- Horizontal Scrubbers
- Vertical Scrubbers
- FWKO / Scrubbers
- Emulsion Treaters
- Flash Treaters
- Steam Separators
- Wellhead separators
Other Technical Articles
As a leader in Slug Catcher design, here are some guidelines every engineer should know.
Choosing the type of Slug Catcher equipment for your next project? This breakdown will help guide your decision.
Understanding the separation methods for your finger-type slug catcher.
WHY US
Taylor Forge Engineered Systems
has continued the reputation of traditionally dependable products
to a variety of industries.
Integrity
We don’t compromise our practices and we won’t cut corners.