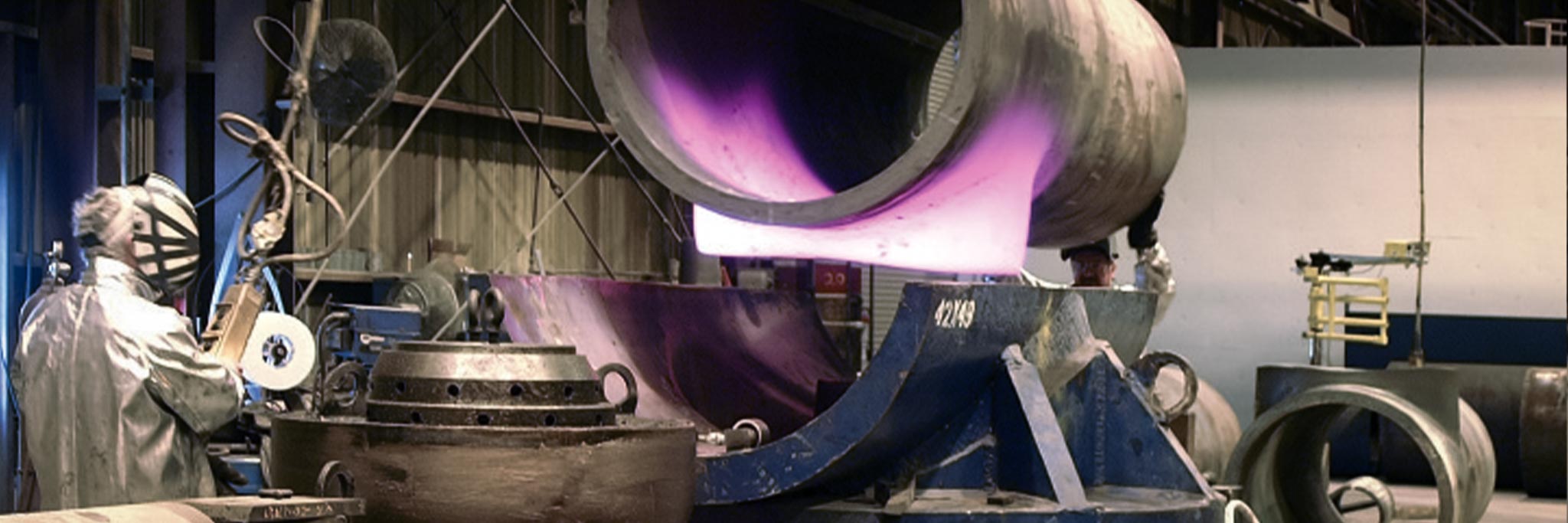
How is an Extruded Outlet Made?
-
- Reinforcement calculations done in accordance with design code & submitted w/ drawings for approval.
- Cut & roll plate. Weld longitudinal seam to complete cylinder.
- Cylinder is laid out with hole locations. Elliptical holes are cut.
- Extrusion area is heated to 1600°F and moved onto outside die.
- Inside die (punch) is threaded onto mandrel protruding through the cut hole.
- Hydraulic press pulls punch through the hole, sometimes multiple pulls required to achieve outlet diameter.
- Header is heat treated as required per the Manufacturing Code.
- Outlets & run ends are machined.
- NDE – plate is UT’d, pilot holes are MT’d, long seams are RT’d
- Finishing activities include Blast and Paint and packaging. Hydrostatic testing is possible, but not recommended to prevent damage to field weld ends.
Heat Treating
Too meet the manufacturing specifications above, all fittings must be supplied in heat treated condition. Depending on the desired mechanical properties and starting material, fittings must be solution annealed, annealed, quench and tempered, or normalized.
Due to the heating elements of the extrusion process, the starting material becomes critical for proper mechanical properties. Ex: API 5L pipe loses mechanical properties during heat treatment.
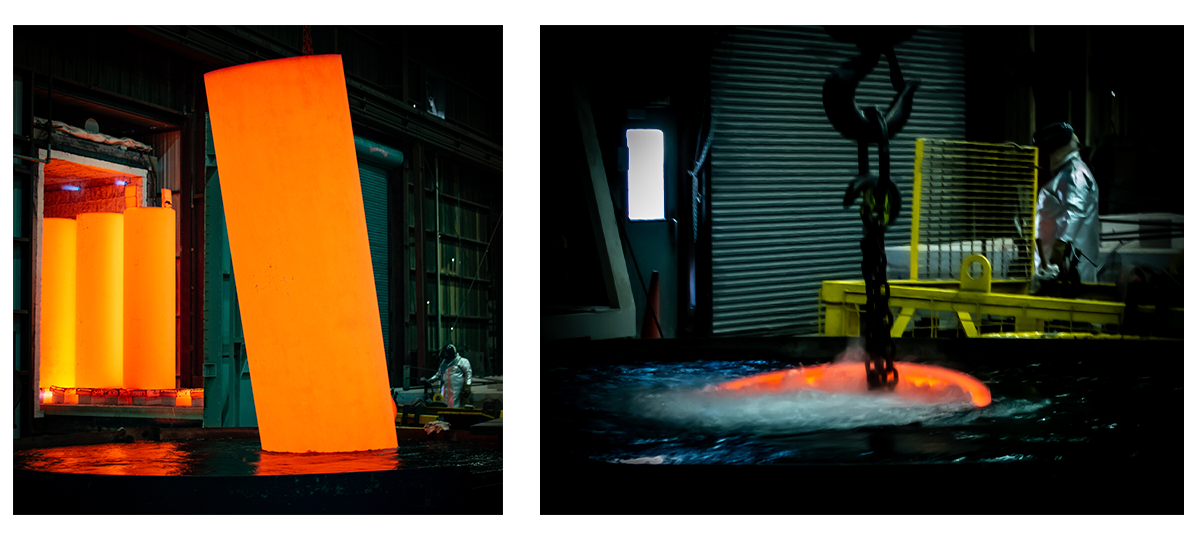
Materials
The materials for your extrusion will ultimately be defined by the codes utilized in your project. A MSS-SP75 fitting manufactured to the pipeline codes, require a base material that meets the MSS-SP75 spec. Similarly, an ASME Section VIII fitting will require a base material from Section 2 of the code.
Manufacturing Capabilities
- Extrusions are typically made from roll and welded plate or pipe up to 84” OD
- Outlets from 1” to 72” OD
- Cylinder wall thicknesses up to 4.0”
- Materials: HSLA up to Y80, chrome alloys, 300 series stainless, nickel alloys, duplex
- Outlets can be pulled radially and tangentially
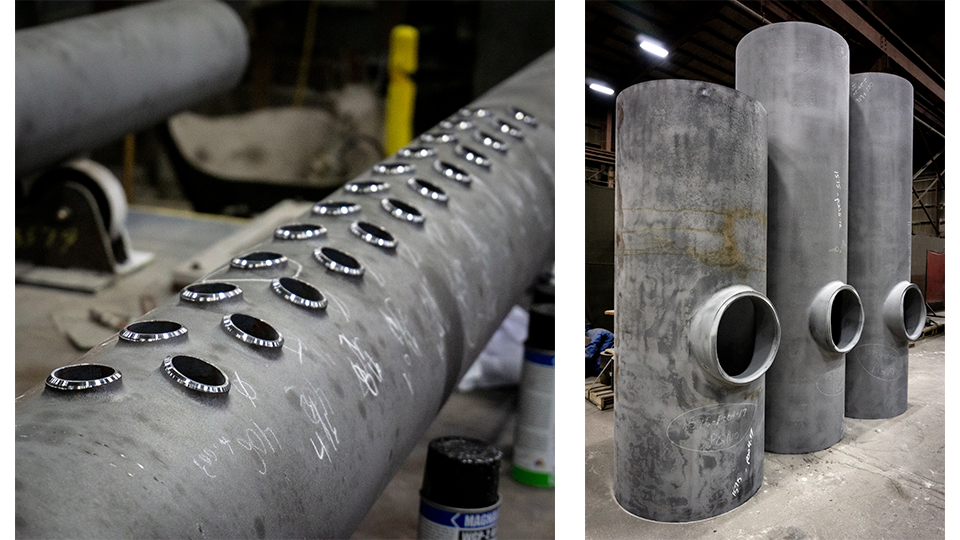
Other Technical Articles
So you’re on a budget? Check out these 5 tips to save money on your next Slug Catcher Project.
As a leader in Slug Catcher design, here are some guidelines every engineer should know.
Choosing the type of Slug Catcher equipment for your next project? This breakdown will help guide your decision.
WHY US
Taylor Forge Engineered Systems
has continued the reputation of traditionally dependable products
to a variety of industries.
Integrity
We don’t compromise our practices and we won’t cut corners.